The following section introduces some example applications. Handles are easy to open from both left and right for the bonnet and cabin door.
YANMAR Technical Review
ViO45/55-6 Product Technology Overview
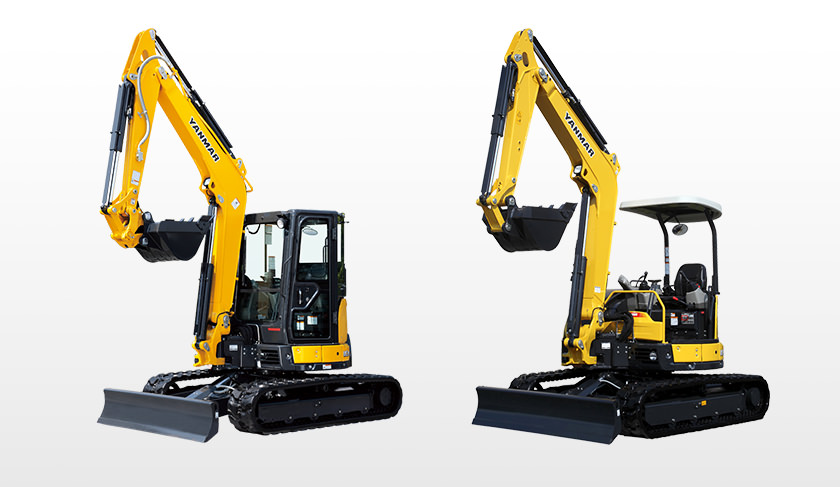
1.Introduction
In 1993, Yanmar led the world by introducing the ViO series of excavators with zero tail swing. The series subsequently underwent a number of full model changes with the Global ViO in 2000 featuring a large space for the operator to provide a comfortable working environment, and the Universal ViO in 2005 being rigorously designed for improved reliability, comfort, and safety. Also, globalization in recent years has seen the products put to a wider range of uses, with increasingly diverse market requirements.
With this background, finding ways to incorporate market feedback and achieve customer’s satisfaction are the keys to expanding market share in the small-class construction machinery industry. Accordingly, Yanmar conducted rigorous market research at the planning stage, and released ViO45/55-6 in 2013, which incorporates features based on customer feedback. The following sections introduce the new models, with five new features including better economy and easier maintenance, along with further enhancements to reliability, comfort, and safety of the Universal ViO.
2. Features
2.1. Economy (Improved Fuel Economy and Digging capacity)
By an optimal output matching between the Yanmar electronically controlled engine and hydraulic pump, and the reviewing of the hydraulic pipe diameter and coupling shapes, hydraulic pressure losses have been reduced.
With this reduction, fuel consumption has been improved approximately 30% compared to the previous model (based on measurements by Yanmar). A further 10% savings can be achieved by using ECO mode. ECO mode reduces fuel consumption across all types of work, by speeding down 300 min-1 of the engine speed from its rated speed. “Auto deceleration” mode also reduces fuel consumption while the machine is in idle. To reduce fuel consumption while the machine is not in use, this mode decelerates the engine to idling speed four seconds after the control levers set to the neutral position. Both modes are included as standard features on all specifications and customers can turn them on or off as required to suit their working conditions and priorities.
The improved excavation cycle time achieved by optimal matching of the combined operating speeds of the boom, arm, and bucket has provided an approximate 10% increase in workload compared to the previous model, while still reducing fuel consumption.
2.2. Maintainability
A “one-touch full open bonnet design” is provided for easier maintenance around the engine, with the rear bonnet and right bonnet being designed to be opened and closed without tools to facilitate routine inspection and other maintenance. Battery replacement can be performed simply by opening the right bonnet and duct bottom cover. Fueling, replenishing hydraulic fluid, and replacement of the air cleaner element can also be performed easily by opening the resin made cover on the right of the machine.
The new models use the same push out flow cooling system for the radiator and oil cooler as the previous models. Corrugated fins are used to ease maintenance. The fins are less likely to get clogged than previous models and are easy to clean.
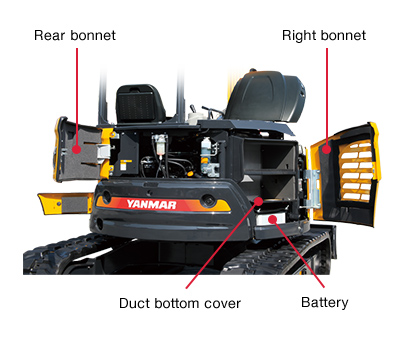
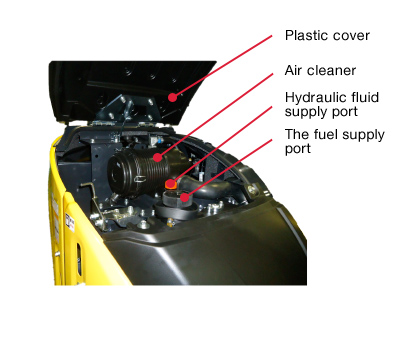
The driver’s seat can also be opened to provide easier access from above for engine head maintenance. Easy access can also be gained to the alternator and starter by removing the front of the seat mount.
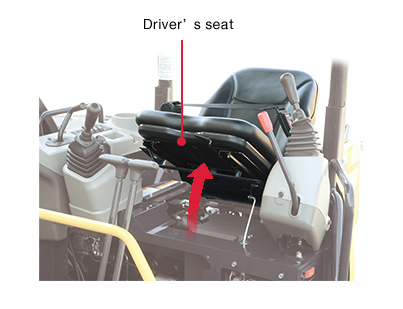
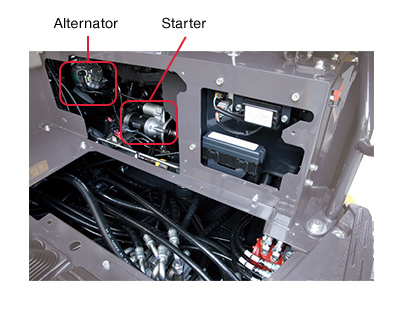
2.3. Comfort
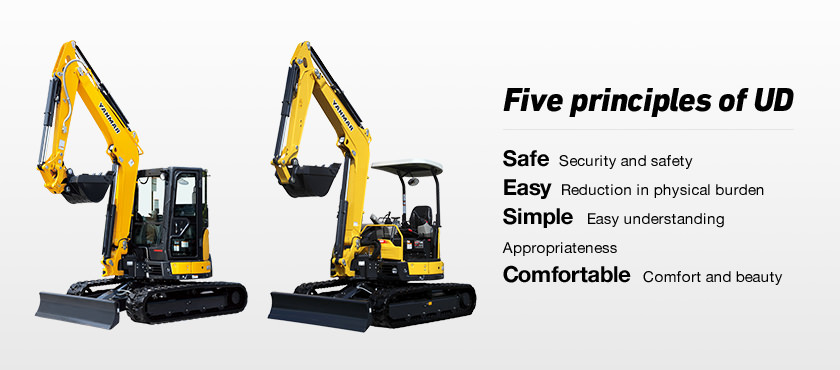
This new model adopted Universal Design (UD) which aims for any operator to operate the machine easily and without any stress. During the planning stage, Yanmar had various non- construction machinery operators evaluate the comfort using previous model, and produced a design based on the five principles of UD that took account of ease-of-use and comfort in all areas, while also making further improvements to comfort.
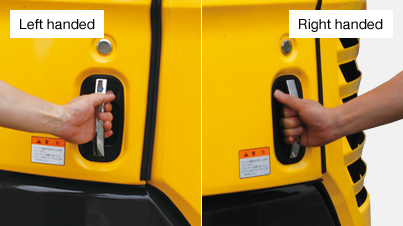
Use of a horizontal open/close mechanism ensures the doors to be opened easily by anyone, regardless of their height. Getting in and out of the cabin has also been facilitated by fitting assist bars that are easy to grasp from any position.
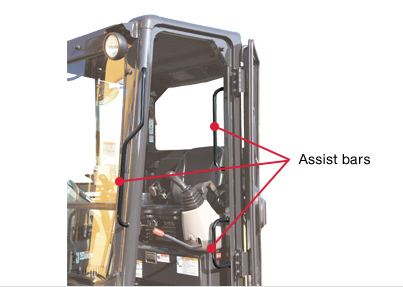
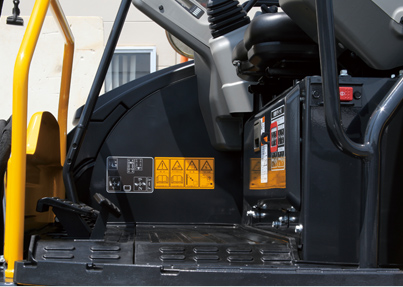
For legroom, a wide space has been provided and steps eliminated to make getting in and out easier. Around the driver’s seat, the large LCD monitor that displays a variety of information and various switches are grouped together on the right of the seat to reduce driver’s workload and fatigue.
A modification of the stroke and operating force and a thorough evaluation of the operators comfort when operating was conducted in order to make the operation smoother for the comfort of the list control lever and blade control lever.
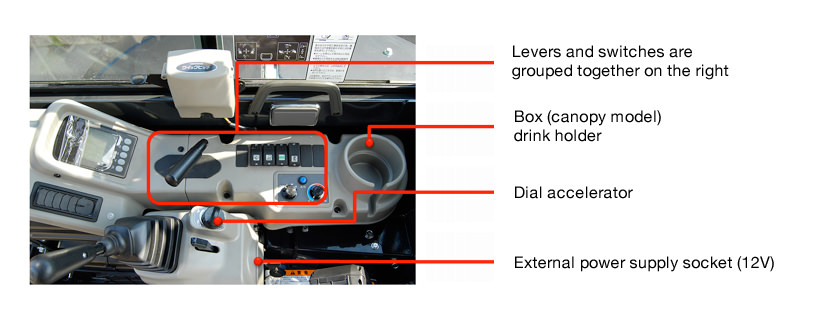
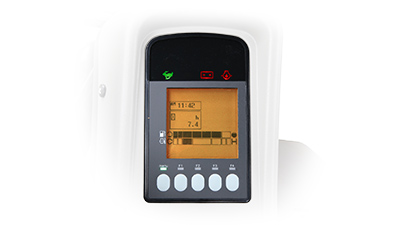
A large 3.3-inch LCD monitor with excellent visibility is included as a standard feature. It is used to display a clock, hour meter, fuel meter, cooling water temperature meter, warning lights, maintenance modes, and so on. It can also manage detailed operaing condition, including monthly operating data and daily operating times, with display of up to three months of operating data available.
SmartAssist Remote is available as an option, which can manage the location data of construction machinery with GPS and communication units via a communication system.
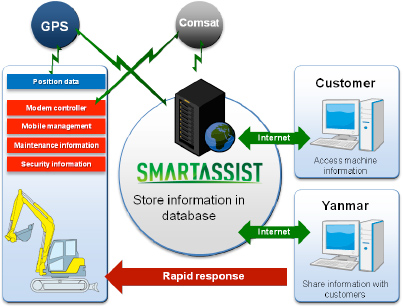
By providing customers with systems that deliver appropriate support at all times through the use of remote monitoring via internet to watch over their construction machinery and quickly identify maintenance times and equipment problems, ensures safer and more trouble-free operation.
2.4. Reliability
Along with product globalization, Yanmar has enhanced undercarriage components to enable use in all area around the world. Through analysis and product testing, wear resistance and part operating life of idlers, sprockets, and track rollers have each been improved by 10% or more compared to previous models.
To extend the life of hydraulic components and reduce engine overheating, cooling performance has been improved by around 15% or more compared to previous models by enlarging the oil cooler and radiator.
By effectively improving the machine longitudinal balance through changes to the component layout, lifting capacity has also been increased.
2.5. Safety
The lightweight two pole canopy complies with TOPS (tip-over protective structure) and head guard standards. The cabin and four pole canopy protect the operator from roll over or falling objects complying with ROPS (roll over protective structure) and FOPS (falling object protective structure) standards.
With regard to environmental features, models for the USA and South Korea are fitted with a Yanmar Tier 4 engine with DPF that complies with the USA’s EPA Tier 4 emission regulations, which are recognized as the most stringent. Models for the Japanese market will also be fitted with this engine from the autumn l of 2015.
The cylinder guard feature, which was well-received on previous models, will also be included as standard on the new series. New boom height limit and arm crowd limits are available as options to enhance safety.
- Boom height limit:For use in location such as sites with overhead cables or where there is a height limit, the operator can optionally specify the height to stop the boom.
- Arm crowd limit:A mechanism for preventing contact with the boom cylinder or other components in situations such as when fitting a breaker.
3. Verification of Product Features
One year after new models were released in the autumn of 2013, the design team conducted market research in Japan and elsewhere to obtain direct feedback from customers. The research aimed to determine whether customers genuinely appreciated the product concept decided on during product development and whether the design deviated in any way from the market needs. As a result, the product overall was well regarded, especially for its maintainability and reliability. It was concluded from this that the product concept was appreciated by the market. However, the research also found that the product still has considerable scope for improvement, with critical comments and requests from some customers. The new VOC obtained through the market research will be valuable information for the next model changes.
4. Conclusions
While this article has only described some of the product features, the design team prioritized customer requests, and incorporated these functions into the excavators, through the market research during the planning stage and after mass production. Although the product development was an extremely difficult one, the excavators went into production and commenced sale in accordance with the original schedule, with help from other divisions within the company. Yanmar is not satisfied with the status quo and intends to continue developing and supplying products that delight its customers.
-IMPORTANT-
The original technical report is written in Japanese.
This document was translated by R&D Management Division.
Author
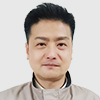
Engineering & Development Dept.
YANMAR CONSTRUCTION EQUIPMENT CO., LTD.